Кто проводит гидро пневмо испытания сосудов. Большая энциклопедия нефти и газа
- Хрупкое разрушение
Данные инструкции выпущены компанией Health and Safety Executive.
Следование инструкциям не обязательно и Вы вправе в Вашей работе принимать другие действия. Но если Вы будете соблюдать правила данных инструкций, Ваших действий будет достаточно, чтобы следовать закону.
ВВЕДЕНИЕ
Данные инструкции предназначены для работодателей, руководителей, начальников участков, индивидуальных потребителей. Они содержат рекомендации по проведению испытаний под давлением, оценке рисков, организации работы и мерам предосторожности.
Приложение основано на научно-исследовательской работе, проведенной компанией HSE, публикация №CRR168 "Безопасность при проведении испытаний под давлением". Работа подготовлена G. Saville, S.M. Richardson, Imperial College of Science, Technology and Medicine вместе с B.J. Skilterne de Bristowe, BJS Research. Работа детально описывает метод расчета опасности при проведении испытаний давлением и расчет размеров защитных ограждений. Информация может быть полезной для организаций, специализирующихся на проведении испытаний или на разработке и производстве ограждений для защиты от потока под давлением и фрагментов оборудования.
ОПРЕДЕЛЕНИЯ
Под термином "оборудование под давлением" в данном документе понимаются сосуды под давлением, элементы трубопровода, системы, содержащие один и более сосуд под давлением, и соответствующую трубную обвязку, а также любая другая емкость, находящаяся под давлением или предназначенная для испытания давлением.
Оборудование под давлением обычно испытывается на гидропрочность, гидроплотность на заключительной стадии производства, после ремонта или модернизации. Также периодическое испытание давлением может быть предусмотрено регламентом регулярного технического контроля.
Термин "испытание давлением" в данном документе включает следующие понятия:
Проверочное испытание давлением: проводится в тех случаях, когда требуемая толщина материала хотя бы одной или нескольких из деталей оборудования под давлением не была рассчитана с достаточной точностью или находится под сомнением. Цель испытания - подтвердить гидропрочность всех деталей и узлов под давлением. Проверочное испытание давлением должно проводиться исключительно опрессовкой жидкостью (гидравлическое испытание) постепенно нарастающим давлением до достижения давления испытания или до возникновения значительных пластических деформаций материала любой детали оборудования под давлением. Метод определения значительных пластических деформаций содержится в Британском Стандарте 5500: 1997, с дополнениями 1998 "Технические требования к резервуарам под давлением без огневого подвода теплоты, изготовленным с применением сварки плавлением".
Стандартное испытание давлением: проводится в том случае, когда требуемая толщина материалов всех деталей и узлов оборудования под давлением подтверждена расчетом с достаточной достоверностью. Цель испытания - подтвердить качество материала деталей оборудования под давлением перед вводом в эксплуатацию. Испытания проводят воздействием давлением, превышающим расчетное давление. Как правило, давление испытания превышает расчетное давление в 1,25 - 1,5 раза.
Испытание на наличие утечек (гидроплотность): может проводиться с превышением расчетного давления не более чем на 10%. Предназначено для испытания деталей, не подлежащих стандартному испытанию давлением. Также может проводиться при более высоких давлениях, не превышающих расчетное давление более чем на 110% при испытании деталей, успешно прошедших стандартное испытание давлением.
Функциональное испытание: проводится опрессовкой рабочей жидкостью с достижением расчетного или рабочего давления. Цель испытания - подтвердить работоспособность оборудования. Испытание может предусматривать приведение в действие движущихся частей оборудования, например открытие, закрытие клапанов, арматуры.
Гидравлические и пневматические испытания
Несмотря на то, что испытание жидкостью (гидравлические испытания) связано с опасностью, это значительно менее опасный метод испытания, чем испытание воздухом, паром или газом (пневматические испытания). Пневматические испытания значительно опаснее из-за большей энергоемкости процесса. Например, выход энергии при потере герметичности оборудования при испытаниях сжатым воздухом в 200 раз превышает выход энергии при испытаниях водой при равных объемах и давлениях.
Пневматические испытания должны проводиться только в тех случаях, когда гидравлические испытания неприменимы. Например, когда недопустимо загрязнение внутренней части оборудования жидкостью или в тех случаях, когда опоры (фундамент) оборудования не рассчитаны на вес оборудования, заполненного жидкостью.
Пневматические испытания на наличие утечек могут быть использованы для выявления малых утечек, наличие которых недопустимо, особенно в оборудовании, предназначенном для работы с воспламеняемыми газами и/или жидкостями.
ОЦЕНКА РИСКОВ
Первый шаг, который необходимо сделать перед началом любых испытаний - проведение оценки рисков при работе оборудования под давлением. При вынесении судебного приговора работодателю оценка рисков является главной мерой достаточности предпринятых мер безопасности при проведении испытаний под давлением. Оценка рисков основана на выявлении всех опасных факторов, оценке рисков, вызванных данными факторами, выработке методов контроля или предотвращения опасных факторов. Более подробную информацию по оценке рисков Вы найдете в соответствующих публикациях HSE, перечисленных в разделе "Список литературы" в конце документа.
В случае, когда испытания проводятся субподрядчиками, необходимо их взаимодействие и координация с производителями оборудования и заказчиками для учета всех возможных рисков.
Оценка рисков укажет объем и состав системы обеспечения безопасности работ, которая должна быть организована перед началом испытаний. Организация системы обеспечения безопасности работ необходима для обеспечения безопасности персонала, вовлеченного в процесс испытаний, а также других людей, находящихся поблизости, включая посторонних лиц.
Оценка рисков также должна определить необходимость наличия специальных ограждений перед установкой во время испытаний, акцентируя внимание на том, при пневматических испытаниях выход энергии многократно больше, чем при гидравлических испытаниях.
Опасные факторы
Основным опасным фактором при испытаниях под давлением является неконтролируемый выход аккумулированной энергии. При пневматических испытаниях выход энергии реализуется в ударной волне потока и в образовании летящих предметов. В случае гидравлических испытаний энергия ударной волны потока незначительна и принимается, что вся энергия расширения переходит в кинетическую энергию летящих предметов.
Следует также учитывать опасные факторы, связанные со сжимаемостью, взрыво- и пожароопасностью, токсичностью подаваемых жидкостей.
Аккумулированная энергия
Оценка рисков при испытаниях под давлением должна учитывать неконтролируемый выход аккумулированной энергии жидкости или газа.
Выход аккумулированной энергии может произойти по следующим причинам:
Хрупкое разрушение деталей оборудования под давлением;
Пластичное разрушение деталей оборудования под давлением;
Отсоединение, отрыв герметизирующих крышек вместе с крепежом, резьбовых фитингов, изолирующих вентилей и т.п.;
Отрыв временных сварных соединений на концах труб, арматуре, патрубках.
Расчет аккумулированной энергии укажет область распространения ударной волны потока и область разлета деталей оборудования в случае их поломки или отрыва. Формула расчета аккумулированной энергии для газа и жидкости дана в приложении к настоящему документу. Более полную информацию Вы найдете в исследовании "Безопасность при испытаниях под давлением".
Ударная волна потока и ее воздействие
Воздействие ударной волны потока на конструкции кратко описано в приложении. Исследование "Безопасность при испытаниях под давлением" описывает физику ударной волны потока, раскрывает вопрос реакции конструкций на динамические нагрузки, вызванные ударной волной потока и ударами деталей оборудования, рассматривает некоторые примеры из практики.
Образование летящих предметов
В приложении описаны способы определения массы, размера, формы, скорости каждого фрагмента. Дана формула расчета толщины стенок ограждения. Более подробная информация и примеры из практики даны в исследовании "Безопасность при испытаниях под давлением".
Возможные модели выхода из строя и, следовательно, размеры фрагментов должны быть согласованы с производителем оборудования.
Хрупкое разрушение
Опасность прорыва оборудования по причине хрупкого разрушения во время испытания должна быть выявлена на этапе проектирования. Этот вопрос должен учитываться при выборе материалов и температур, при которых проводятся испытания.
Cтраница 1
Гидравлические и пневматические испытания служат для проверки плотности швов. Гидравлическое испытание позволяет установить также прочность изделия. Гидравлическое испытание производится следующим образом: сваренный сосуд наполняют водой, затем с помощью гидравлического насоса создают в сосуде давление, превышающее в полтора раза максимальное рабочее давление для данного сосуда. После выдержки в течение 5 мин давление в сосуде снижают до рабочего и производят легкое обстукивание швов молотком весом в 1 кг. Запотевшие участки сварных швов или участки, дающие течь, отмечают как дефектные. После снижения давления в сосуде до атмосферного дефектные швы вырубают и заваривают вновь.
Гидравлическое и пневматическое испытание отдельных узлов и секций трубопроводов (до их монтажа) проводят с соблюдением специальных требований, оговоренных в проекте или заказе.
Гидравлическое и пневматическое испытание сложных узлов металлоконструкций, работающих иод давлением. Устранение дефектов, обнаруженных после испытания сложных узлов металлоконструкций.
Гидравлические и пневматические испытания проводят под наблюдением ответственного лица.
Гидравлическое и пневматическое испытание сложных узлов металлоконструкций, работающих под давлением. Устранение дефектов, обнаруженных после испытания сложных узлов металлоконструкций.
Гидравлические и пневматические испытания оборудования для сварки более индивидуальны и сводятся в основном к несложным методам определения герметичности и необходимых норм давления и расхода газа или воды.
Гидравлические и пневматические испытания дюкеров, уложенных через сухие овраги, могут производиться одновременно с соседними участками трубопровода.
Гидравлические и пневматические испытания корпусов аппаратов ведут в соответствии с указаниями главы IV. Перемешивающие устройства должны быть подвергнуты индивидуальным испытаниям вхолостую, а затем под нагрузкой для проверки правильности сборки движущихся частей, приработки трущихся поверхностей, регулировки работы всех узлов и систем аппарата. До начала обкатки в помещении должны быть полностью закончены отделочные работы и монтаж трубопроводов и конструкций, связанных с данным аппаратом.
Гидравлические и пневматические испытания емкостной аппаратуры производятся в соответствии с указаниями главы I настоящего раздела.
Гидравлическое и пневматическое испытания имеют целью проверить плотность и прочность корпуса аппарата или сосуда, а также разъемных его соединений. Величина гидравлического давления должна быть указана в монтажных чертежах и технических условиях. При этом следует иметь в виду, что аппараты и сосуды, работающие под давлением более 0 7 ати, подлежат надзору инспекции Гос-гортехнадзора; гидравлическое и пневматическое испытания таких аппаратов производятся согласно правилам этой организации.
Гидравлическое и пневматическое испытания вертикальных изотермических резервуаров для хранения жидкого аммиака должны производиться в соответствии с указаниями проекта. Пневматическое испытание резервуара разрешается производить воздухом.
Гидравлическому и пневматическому испытанию подвергаются трубопроводы для газообразного и жидкого аммиака независимо от давления среды и диаметра труб.
Гидравлическим и пневматическим испытаниям подвергают сигнализаторы давления, скоростные и объемные счетчики количества жидкости, дифманометры мембранные или сильфонные, реле уровня.
Страница 12 из 16
ПНЕВМАТИЧЕСКИЕ ИСПЫТАНИЯ
8.10. Выполнение пневматических испытаний следует производить для стальных трубопроводов с рабочим давлением не выше 1,6 МПа (16 кгс/см 2) и температурой до 250° С, монтируемых из труб и деталей, испытанных на прочность и герметичность (плотность) заводами-изготови-телями в соответствии с ГОСТ 3845-75 (при этом заводское испытатель-ное давление для труб, арматуры, оборудования и других изделий и дета-лей трубопровода должно быть на 20% выше испытательного давления, принятого для смонтированного трубопровода).
Установка чугунной арматуры (кроме вентилей из ковкого чугуна) на время испытаний не допускается.
8.11. Заполнение трубопровода воздухом и подъем давления следует производить плавно со скоростью не более 0,3 МПа (3 кгс/см 2) в 1 ч. Визуальный осмотр трассы (вход в охранную [опасную) зону, но без спуска в траншею] допускается при величине давления, равной 0,3 испы-тательного, но не более 0,3 МПа (3 кгс/см 2).
На период осмотра трассы подъем давления должен быть прекращен.
При достижении величины испытательного давления трубопровод дол-жен быть выдержан для выравнивания температуры воздуха по длине тру-бопровода. После выравнивания температуры воздуха испытательное дав-ление выдерживается 30 мин и затем плавно снижается до 0,3 МПа (3 кгс/см 2), но не выше величины рабочего давления теплоносителя; при этом давлении производится осмотр трубопроводов с отметкой дефект-ных мест.
Места утечки определяются по звуку просачивающегося воздуха, по пу-зырям при покрытии сварных стыков и других мест мыльной эмульсией и применением других методов.
Дефекты устраняются только при снижении избыточного давления до нуля и отключении компрессора.
8.12. Результаты предварительных пневматических испытаний счита-ются удовлетворительными, если во время их проведения не произошло падения давления по манометру, не обнаружены дефекты в сварных швах, фланцевых соединениях, трубах, оборудовании и других элементах и из-делиях трубопровода, отсутствуют признаки сдвига или деформации тру-бопровода и неподвижных опор.
8.13. Трубопроводы водяных сетей в закрытых системах теплоснабже-ния и конденсатопроводы должны быть, как правило, подвергнуты гидропневматической промывке.
Допускается гидравлическая промывка с повторным использованием промывочной воды путем пропуска ее через временные грязевики, устанавливаемые по ходу движения воды на концах подающего и обратного трубопроводов.
Промывка, как правило, должна производиться технической водой. Допускается промывка хозяйственно-питьевой водой с обоснованием в проекте производства работ.
8.14. Трубопроводы водяных сетей открытых систем теплоснабжения и сетей горячего водоснабжения необходимо промывать гидропневматическим способом водой питьевого качества до полного осветления промы-вочной воды. По окончании промывки трубопроводы должны быть про-дезинфицированы путем их заполнения водой с содержанием активного хлора в дозе 75-100 мг/л при времени контакта не менее 6 ч. Трубопро-воды диаметром до 200 мм и протяженностью до 1 км разрешается, по со-гласованию с местными органами санитарно-эпидемиологической службы, хлорированию не подвергать и ограничиться промывкой водой, соответст-вующей требованиям ГОСТ 2874-82.
После промывки результаты лабораторного анализа проб промывной воды должны соответствовать требованиям ГОСТ 2874-82. О результатах промывки (дезинфекции) санитарно-эпидемиологической службой состав-ляется заключение.
8.15. Давление в трубопроводе при промывке должно быть не выше ра-бочего. Давление воздуха при гидропневматической промывке не должно превышать рабочее давление теплоносителя и быть не выше 0,6 МПа (6 кгс/см 2).
Скорости воды при гидравлической промывке должны быть не ниже расчетных скоростей теплоносителя, указанных в рабочих чертежах, а при гидропневматической - превышать расчетные не менее чем на 0,5 м/с.
8.16. Паропроводы должны быть продуты паром со сбросом в атмосфе-ру через специально установленные продувочные патрубки с запорной ар-матурой. Для прогрева паропровода перед продувкой должны быть открыты все пусковые дренажи. Скорость прогрева должна обеспечивать отсутст-вие гидравлических ударов в трубопроводе.
Скорости пара при продувке каждого участка должны быть не менее рабочих скоростей при расчетных параметрах теплоносителя.
Содержание |
---|
5. ГИДРАВЛИЧЕСКИЕ (ПНЕВМАТИЧЕСКИЕ) ИСПЫТАНИЯ
5.1. Общие требования
5.1.1. Гидравлические (пневматические) испытания проводят с целью проверки прочности и плотности оборудования, трубопроводов, их деталей и сборочных единиц, нагружаемых давлением. 5.1.2. Гидравлические испытания проводят: 1) после изготовления предприятием-изготовителем оборудования или элементов трубопроводов, поставляемых на монтаж; 2) после монтажа оборудования и трубопроводов; 3) в процессе эксплуатации оборудования и трубопроводов, нагружаемых давлением воды, пара или пароводяной смеси. 5.1.3. Допускается вместо гидравлических испытаний проводить пневматические испытания оборудования и трубопроводов, нагружаемых давлением газа, работающих под вакуумом, находящихся в контакте с жидкометаллическим теплоносителем, а также страховочных корпусов (кожухов) АЭУ с реакторами на быстрых нейтронах и защитных оболочек ACT. Возможность такой замены должна быть одобрена с Госатомнадзором России. Допускается не проводить гидравлические испытания (после изготовления и в процессе эксплуатации) корпусов опытных и исследовательских ядерных реакторов, работающих под давлением веса наполняющей их жидкости, при условии проведения в процессе изготовления 100%-ного контроля сварных швов ультразвуковой дефектоскопией или радиографическим методом и методами поверхностной дефектоскопии. 5.1.4. Гидравлические (пневматические) испытания после монтажа и в процессе эксплуатации проводятся в сроки, указанные в п. 8.2.6. 5.1.5. Проведение гидравлических (пневматических) испытаний после монтажа при сдаче оборудования и трубопроводов в эксплуатацию, а также в процессе эксплуатации (за исключением случаев ремонта, специально оговоренных в настоящем документе), является обязательным. 5.1.6. Проведение гидравлических испытаний деталей или сборочных единиц трубопроводов, изготовленных на монтажных площадках, допускается совмещать с гидравлическими испытаниями после завершения монтажа. 5.1.7. Оборудование и трубопроводы после изготовления и монтажа должны подвергаться гидравлическим испытаниям до нанесения защитных антикоррозионных покрытий или тепловой изоляции. На оборудовании и трубопроводах, в процессе эксплуатации контактирующих с жидкометаллическим теплоносителем, допускается нанесение тепловой изоляции до гидравлических испытаний указанным теплоносителем. Допускается проводить металлизацию (без нанесения лакокрасочных покрытий) сварных соединений трубопроводов до гидравлических испытаний, если это невозможно провести после окончания монтажа, что должно быть оговорено в конструкторской документации. 5.1.8. Гидравлические (пневматические) испытания оборудования и трубопроводов в процессе эксплуатации должны проводиться после снятия тепловой изоляции в местах, указанных в п. 2.1.9, а также оговоренных в конструкторской документации. 5.1.9. Гидравлические испытания отдельных деталей и сборочных единиц оборудования и трубопроводов после их изготовления допускается не проводить в следующих случаях: 1) предприятие-изготовитель осуществляет гидравлические испытания этих деталей и сборочных единиц в составе укрупненных сборочных единиц или изделий; 2) предприятие-изготовитель не содержащего сварных соединений I и I и категории оборудования группы В из сталей перлитного класса или высокохромистых сталей осуществляет сплошной ультразвуковой и радиографический контроль основного металла и сварных соединений, а из сталей аустенитного класса и железоникелевых сплавов - сплошной радиографический контроль основного металла и сварных соединений при соблюдении всех других требований ПК и конструкторской документации; 3) предприятие-изготовитель оборудования группы С из сталей перлитного класса и из высокохромистых сталей осуществляет сплошной ультразвуковой контроль всех сварных соединений, а также их радиографический контроль в удвоенном объеме по сравнению с предусмотренным ПК, а из сталей аустенитного класса и железоникелевых сталей - сплошной радиографический контроль всех сварных соединений; при этом должны соблюдаться все другие требования ПК и конструкторской документации; 4) предприятие-изготовитель деталей и сборочных единиц трубопроводов групп В и С из сталей перлитного класса и из высокохромистых сталей осуществляет сплошной ультразвуковой контроль всех сварных соединений, а также радиографический контроль сварных соединений II а, II на категорий в объеме 100%, II в, II нв и III а категорий - в объеме 50%, III в - в объеме 25%, а из сталей аустенитного класса - сплошной радиографический контроль всех сварных соединений, при этом должны соблюдаться все другие требования ПК и конструкторской документации; кроме того, должен быть проведен дополнительный капиллярный или магнитопорошковый контроль механически обработанных поверхностей (расточек, переходов, гибов труб и т. и.) и ультразвуковой или радиографический контроль металла в зонах концентрации напряжений и в зонах, подвергавшихся деформации более 5% при изготовлении (гибов и раздаваемых концов труб, вытянутых горловин и т.п.) и в объеме, устанавливаемом конструкторской документацией (для трубопроводов группы С указанный дополнительный контроль допускается не проводить). 5.1.10. Нормы оценки качества при контроле по п. 5.1.9 должны приниматься для основного металла по стандартам или техническим условиям на соответствующие материалы и полуфабрикаты, а для сварных соединений - по ПК. 5.1.11. Гидравлические (пневматические) испытания отдельных деталей (например, труб) на предприятии-изготовителе допускается не проводить, если они прошли гидравлические испытания на предприятии-поставщике этих изделий и после этого не подвергались операциям, в процессе которых материал указанных деталей претерпевал пластические деформации. 5.1.12. Гидравлические (пневматические) испытания после изготовления элементов оборудования и трубопроводов, нагружаемых в процессе эксплуатации наружным давлением, допускается проводить при нагружении внутренним давлением.5.2. Определение давления гидравлических (пневматических) испытаний
5.2.1. Давление гидравлических испытаний должно быть не менее определяемого по формуле:(нижняя граница)
И не более давления, при котором в испытуемом изделии возникнут общие мембранные напряжения, равные 1,35 [ ] Th , а сумма общих или местных мембранных и общих изгибных напряжений достигнет 1,7 [ ] Th (верхняя граница). В вышеприведенной формуле К = 1,25 для оборудования и трубопроводов и К = 1 для защитных оболочек и страховочных корпусов (кожухов), Р - расчетное давление при испытаниях на предприятии-изготовителе или рабочее давление при испытаниях после монтажа и в процессе эксплуатации, [ ] Th - номинальное допустимое напряжение при температуре гидравлических испытаний T h для рассматриваемого элемента конструкции, [ ] T - номинальное допускаемое напряжение при расчетной температуре Т рассматриваемого элемента конструкции. Для элементов, нагружаемых наружным давлением, должно также выполняться условие:
Р h 1,25 [Р ].
Примечание. Значения [ ] Th , [ ] T , общие и местные мембранные и общие изгибные напряжения; [Р ] - допускаемое наружное давление при температуре гидравлических испытаний определяют по Нормам расчета на прочность. 5.2.2. При давлении Р до 0,49 МПа (5 кгс/см 2) значение Р h должно быть более 1,5Р, но не менее 0,2 МПа (2 кгс/см 2). При давлении Р более 0,49 МПа (5 кгс/см 2) значение P h должно определяться из условий п. 5.2.1, но быть не менее (Р + 0,29) МПа ((Р + 3) кгс/см 2). Указанные требования не распространяются на оборудование и трубопроводы с жидкометаллическим теплоносителем. 5.2.3. В случае, если гидравлическим (пневматическим) испытаниям подвергаются система или контур, состоящие из оборудования и трубопроводов, работающих при разных рабочих давлениях и (или) расчетных температурах, или изготовленных из материалов с различными [ ] Th и (или) [ ] T , то давление гидравлических (пневматических) испытаний этой системы (контура) следует принимать равным минимальному значению верхней границы давлений испытаний, выбранному из всех соответствующих значений для оборудования и трубопроводов, составляющих систему (контур). 5.2.4. Значения давления гидравлических испытаний для оборудования и сборочных единиц (блоков) трубопроводов должны указываться предприятием-изготовителем в паспорте оборудования и свидетельстве об изготовлении деталей и сборочных единиц трубопровода. Значения давлений гидравлических (пневматических) испытаний систем (контуров) должны определяться проектной организацией и сообщаться предприятию-владельцу оборудования и трубопроводов, которое уточняет эти значения на основе данных, содержащихся в паспортах оборудования и трубопроводов, комплектующих систему (контур).
5.3. Определение температуры гидравлических (пневматических) испытаний
5.3.1. Гидравлические (пневматические) испытания оборудования и трубопроводов должны проводиться при температуре испытательной среды, при которой температура металла испытуемого оборудования и трубопроводов не будет ниже минимальной допускаемой, определяемой согласно Нормам расчета на прочность. При этом во всех случаях температура испытательной и окружающей среды не должна быть ниже 5 °С. 5.3.2. Допускается проведение гидравлических (пневматических) испытаний после изготовления или монтажа без проведения расчета по п. 5.3.1 при температуре металла не менее 5 °С в следующих случаях: 1) изделие изготовлено из коррозионно-стойкой стали аустенитного класса, цветного или железоникелевого сплава; 2) изделие изготовлено из материалов с пределом текучести при температуре 20 °С менее 295 МПа (30 кгс/мм 2) и имеет наибольшую толщину стенки не более 25 мм; 3) изделие изготовлено из материалов с пределом текучести при температуре 20 °С менее 590 МПа (60 кгс/мм 2) и. имеет наибольшую толщину стенки не более 16 мм. Допускается также без проведения расчета по п. 5.3.1 определять минимальную допускаемую температуру металла при гидравлических испытаниях T h из следующих соотношений: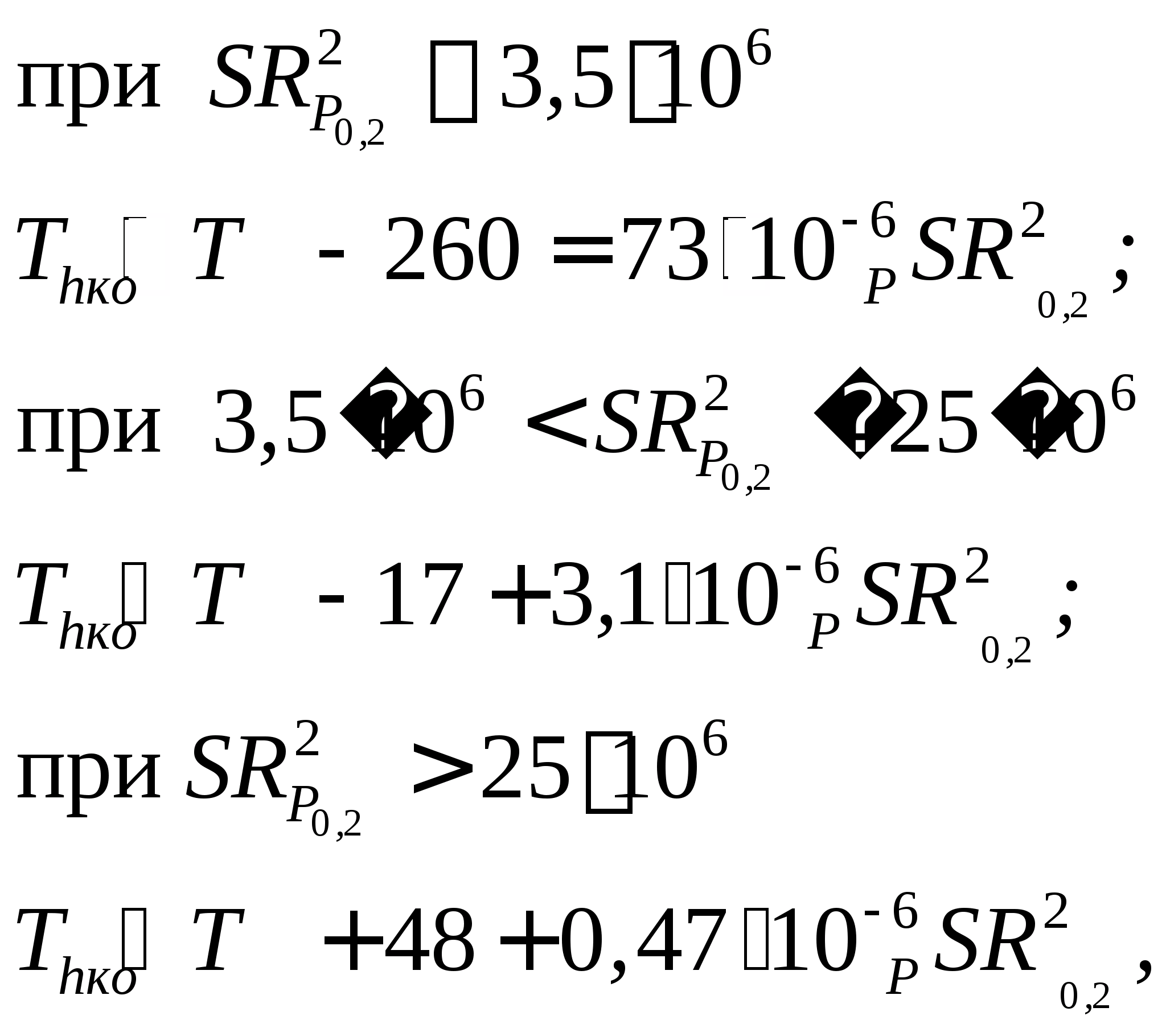
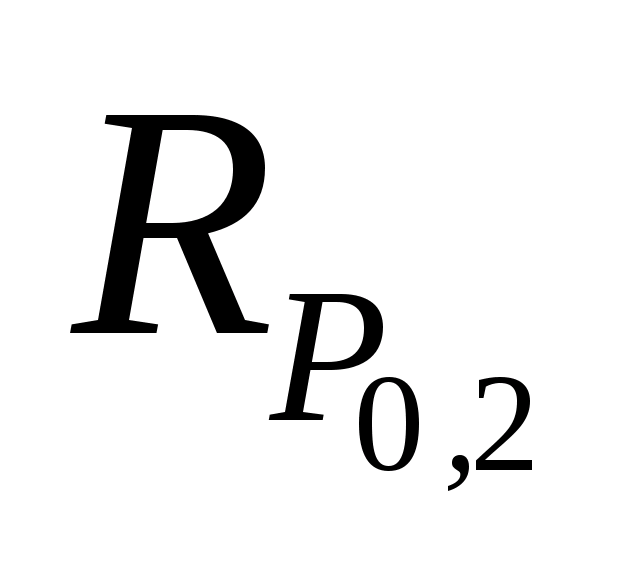
5.4. Требования к проведению гидравлических (пневматических) испытаний
5.4.1. Время выдержки оборудования и трубопроводов под давлением Р h при гидравлических испытаниях должно быть не менее 10 мин. После выдержки давление гидравлических испытаний снижается до значений 0,8Р h и проводится осмотр оборудования и трубопроводов в доступных местах в течение времени, необходимого для осмотра. Минимально допускаемая температура металла при выдержке должна определяться по нормам расчета на прочность. Измерение давления при гидравлических испытаниях должно проводиться по двум независимым поверенным манометрам или каналам измерений. Погрешность измерения давления при гидравлических испытаниях с учетом класса точности датчика (манометра) не должна превышать ± 5% номинального значения давления испытаний. Класс точности датчика (манометра) должен быть не менее 1,5. 5.4.2. Время выдержки под давлением P h при испытаниях после изготовления арматуры с внутренним диаметром присоединительных патрубков не более 100 мм допускается устанавливать по технической документации на изделие. 5.4.3. В процессе гидравлических испытаний допускается колебание давления вследствие изменения температуры жидкости. Допускаемые значения колебаний температуры и давления в каждом конкретном случае должно устанавливаться расчетом или экспериментально, при этом давление не должны выходить за нижнюю и верхнюю границы по п. 5.2.1, 5.2.3. Понижение температуры ниже устанавливаемой по п. 5.3 не допускается. Допускается компенсировать предусмотренные конструкцией уплотнений валов насосов протечки путем подкачки испытательной среды. 5.4.4. Гидравлические испытания должны проводиться с использованием негорючей среды, не оказывающей вредного влияния на оборудование или трубопровод. Требования к качеству испытательной среды устанавливаются техническими условиями на изделие и должны указываться в паспортах оборудования и трубопроводов или в свидетельствах об изготовлении деталей и сборочных единиц трубопроводов. 5.4.5. Контроль температуры металла должен проводиться приборами термоконтроля. Контроль температуры допускается не проводить, если температура жидкости и температура окружающей среды выше температуры гидравлических испытаний, установленной по п. 5.3 Температура должна контролироваться датчиками и приборами с суммарной погрешностью, не превышающей ± 3% максимального значения измеряемой температуры. 5.4.6. При проведении гидравлических испытаний оборудования и трубопроводов должны быть приняты меры для исключения скопления газовых пузырей в полостях, заполненных жидкостью.5.5. Пневматические испытания
5.5.1. Давление пневматических испытаний Р р должно быть не менее определяемого по формуле: (нижняя граница),
Где К р = 1,15 для оборудования и трубопроводов; К р = 1 для защитных оболочек и страховочных корпусов (кожухов). Верхняя граница та же, что и в п. 5.2.1. Для элементов, нагружаемых наружным давлением, должно выполняться также условие
Требования п. 5.2.2 при пневматических испытаниях не имеют силы. 5.5.2. Если в оборудовании и трубопроводах в процессе эксплуатации имеется столб жидкого металла, который невозможно иметь в процессе пневматических испытаний, то нижняя граница давления пневматических испытаний должна определяться по формуле
Где Н - высота столба жидкого металла; - удельная масса жидкого металла при расчетной температуре; Р - рабочее давление газа над уровнем жидкого металла. 5.5.3. При пневматических испытаниях защитных оболочек, страховочных корпусов (кожухов) охватываемые ими оборудование или трубопроводы могут находиться под наружным давлением, вследствие чего в оборудовании или трубопроводах может оказаться необходимым создавать противодавление P g . В этом случае должно выполняться следующее условие:
5.5.4. При определении минимально допустимой температуры металла следует руководствоваться указаниями п. 5.3. 5.5.5. При пневматических испытаниях должны соблюдаться требования п. 5.2.3, 5.2.4, 5.3, 5.4.1 (в части требований к погрешности и измерений и класса точности прибора), п. 5.4.3, 5.4.5. 5.5.6. Время выдержки оборудования и трубопроводов под давлением Р р при пневматических испытаниях должно быть не менее 30 мин. После выдержки давление снижается, и проводится осмотр оборудования и трубопроводов в доступных местах в течение необходимого времени. Осмотр проводится при давлении, определяемом лицом, ответственным за проведением испытаний исходя из условий безопасности, но во всех случаях это давление не должно превышать 0,85Р р . Время выдержки под давлением арматуры с внутренним диаметром присоединительных патрубков не более 100 мм при пневматических испытаниях устанавливается техническими условиями на поставку. 5.5.7. Предназначенные для пневматических испытаний вентили наполнительного трубопровода и приборы измерения давления и температуры должны быть выведены за пределы помещения, в котором находится испытываемое оборудование, в безопасное для персонала место. Во время подъема давления газа в испытываемом оборудовании и трубопроводах, выдержки под давлением Р р и снижения давления до значения, установленного для осмотра, персонал должен находиться в безопасном месте.
5.6. Программы проведения гидравлических (пневматических) испытаний
5.6.1. Перед проведением гидравлических (пневматических) испытаний оборудования и сборочных единиц (деталей) трубопроводов предприятием-изготовителем должна быть составлена производственная программа (или технологическая инструкция, технологический процесс) испытаний. 5.6.2. Для проведения гидравлических (пневматических) испытаний после монтажа и в процессе эксплуатации проектной организацией должна быть составлена комплексная программа испытаний, на основе которой администрацией АЭУ (или специализированной организацией, определяемой решением соответствующего министерства) должна быть составлена рабочая программа испытаний. (Измененная редакция. Изм. № 1). 5.6.3. Производственная программа (технологическая инструкция, технологический процесс) гидравлических (пневматических) испытаний оборудования и сборочных единиц (деталей) трубопроводов после изготовления должна включать следующие данные: 1) наименование оборудования или сборочных единиц (деталей) трубопроводов; 2) расчетное давление; 3) давление гидравлических (пневматических) испытаний; 4) температура гидравлических (пневматических) испытаний; 5) испытательные среды и требования к их качеству; 6) допустимые скорости повышения и снижения давления; 7) допустимые скорости повышения и снижения температуры; 8) время выдержки при давлении испытаний P h (P p ); 9) давление, при котором должен проводиться осмотр; 10) источник давления; 11) метод нагрева испытательной среды (при необходимости); 12) точки установки датчиков (приборов) контроля давления и их класс точности; 13) точки установки датчиков (приборов) контроля температур и их класс точности; 14) допускаемые пределы колебания давления и температуры в процессе выдержки; 15) требования по технике безопасности; 16) места установки технологических заглушек; 17) перечень организационных мероприятий, включая назначение ответственных за испытания лиц. Программа должна быть утверждена главным инженером (директором) предприятия-изготовителя и согласована с соответствующей конструкторской организацией. 5.6.4. Комплексная программа гидравлических (пневматических) испытаний систем, их частей или отдельных видов оборудования и трубопроводов после монтажа и в процессе эксплуатации должна включать следующие данные: 1) наименование и границы испытуемой системы (части системы, оборудования, трубопроводов); 2) рабочее давление; 3) давление гидравлических (пневматических) испытаний; 4) температура гидравлических (пневматических) испытаний; 5) испытательные среды и требования к их качеству; 6) допустимые скорости повышения и понижения давления; 7) допустимые скорости повышения и понижения температуры; 8) давление, при котором должен проводиться осмотр; 9) способы заполнения и дренирования испытательной среды; 10) источник создания давления; 11) метод нагрева испытательной среды (при необходимости); 12) точки установки датчиков (приборов) контроля давления; 13) точки установки датчиков (приборов) контроля температуры; 14) допускаемые пределы колебания давления и температуры в процессе выдержки. Комплексная программа должна быть согласована руководством проектной организации и утверждена администрацией АЭУ. (Измененная редакция. Изм. № 1). 5.6.5. Рабочая программа гидравлических (пневматических) испытаний помимо сведений, перечисленных в п. 5.6.4, должна содержать следующие данные: 1) уточнение по паспортам комплектующих испытуемых оборудования и трубопроводов значений давления и температуры гидравлических (пневматических) испытаний; 2) место подключения источника давления; 3) перечень используемых датчиков и приборов контроля давления и температуры с указанием класса точности; 4) график проведения испытаний (ступени подъема и сброса давления, подъема и снижения температуры, время выдержки и т.п.); 5) способы контроля состояния испытуемого оборудования и трубопроводов в процессе осмотра и после завершения испытаний; 6) меры по подготовке к проведению испытаний (с указанием перекрываемой и открываемой арматуры, ограничивающей испытуемую систему или ее часть); 7) перечень мест снятия тепловой изоляции; 8) меры защиты от превышения давления свыше испытательного; 9) требования по технике безопасности; 10) организационные мероприятия (включая назначение ответственного за испытания лица); 11) номер комплексной программы, на основе которой составлена рабочая программа. Рабочая программа должна быть утверждена администрацией АЭУ. (Измененная редакция. Изм. № 1). 5.6.6. После завершения испытаний должен быть составлен протокол, включающий следующие данные: 1) наименование предприятия, проводившего испытания; 2) наименование испытанной системы (части системы, оборудования, трубопроводов, сборочных единиц, деталей); 3) расчетное (рабочее) давление; 4) расчетные температуры; 5) давление испытаний; 6) температура испытаний; 7) испытательная среда; 8) время выдержки при давлении испытаний; 9) давление, при котором проводится осмотр; 10) номер рабочей (производственной) программы; 11) результат испытаний; 12) подпись ответственного лица и дата.5.7. Оценка результатов гидравлических (пневматических) испытаний
Оборудование и трубопроводы считаются выдержавшими гидравлические (пневматические) испытания, если в процессе испытаний и при осмотре не обнаружено течей и разрывов металла, в процессе выдержки по п. 3.4.1 падение давления не выходило за пределы, указанные в п. 5.4.3, а после испытаний не выявлено видимых остаточных деформаций. При гидравлических (пневматических) испытаниях оборудования и сборочных единиц (деталей) трубопроводов течи через технологические уплотнения, предназначенные для проведения испытаний, не являются браковочным признаком.